ÁCIDO SULFÚRICO
El ácido sulfúrico, aceite de vitriolo, espíritu de vitriolo, licor de vitriolo o tetraoxosulfato (VI) de hidrógeno es un compuesto químico muy corrosivo cuya fórmula es H2SO4. Es el compuesto químico que más se produce en el mundo, por eso se utiliza como uno de los tantos medidores de la capacidad industrial de los países. Una gran parte se emplea en la obtención de fertilizantes. También se usa para la síntesis de otros ácidos y sulfatos y en la industria petroquímica.
Generalmente se obtiene a partir de óxido de azufre (IV), por oxidación con óxidos de nitrógeno en disolución acuosa. Normalmente después se llevan a cabo procesos para conseguir una mayor concentración del ácido. Antiguamente se lo denominaba aceite o espíritu de vitriolo, porque se producía a partir de este mineral.
La molécula presenta una estructura piramidal, con el átomo de azufre en el centro y los cuatro átomos de oxígeno en los vértices. Los dos átomos de hidrógeno están unidos a los átomos de oxígeno no unidos por enlace doble al azufre. Dependiendo de la disolución, estos hidrógenos se pueden disociar. En agua se comporta como un ácido fuerte en su primera disociación, dando el anión hidrogenosulfato, y como un ácido débil en la segunda, dando el anión sulfato.
Además reacciona violentamente con agua y compuestos orgánicos con desprendimiento de calor.
El Ácido Sulfúrico, de fórmula H2SO4 ( óleum: H2SO4 con SO3 en solución), a temperatura ambiente es un líquido corrosivo, es más pesado que el agua e incoloro (a temperatura y presión ambiente). El óleum tiene un olor picante y penetrante. Esta es la sustancia más importante de la industria química mundial. Sus nombres químicos son ácido sulfúrico y ácido sulfúrico fumante. También es llamado aceite de vitriolo, ácido de baterías y ácido de fertilizantes.
El ácido sulfúrico es un ácido diprótico, ya que cada unidad de ácido produce dos iones H en dos etapas independientes:
H2SO4 (ac) H (ac) + HSO4 (ac)
HSO4 (ac) H (ac) + SO4 (ac)
La materia prima para la fabricación de ácido sulfúrico es gas limpio de dióxido de azufre (SO2). Este gas viene de: quemado de azufre fundido como subproducto, tostación o fundición de concentrados de sulfuros metálicos y descomposición de catalizadores de ácido sulfúrico de procesos químicos orgánicos.
Se requiere una limpieza eficiente para gases de descomposición ácida contaminados y metalúrgicos, especialmente estos primeros.
El ácido sulfúrico se obtiene a partir de SO2 por medio de: oxidación de SO2(g) a SO3(g) en contacto con un catalizador soportado en fase líquida, seguido de reacción del SO3(g) resultante con la solución al 98.5% de ácido sulfúrico y 1.5% de agua.
Se requiere una limpieza eficiente para gases de descomposición ácida contaminados y metalúrgicos, especialmente estos primeros.
El ácido sulfúrico se obtiene a partir de SO2 por medio de: oxidación de SO2(g) a SO3(g) en contacto con un catalizador soportado en fase líquida, seguido de reacción del SO3(g) resultante con la solución al 98.5% de ácido sulfúrico y 1.5% de agua.
Este artículo discute las razones para estos pasos de proceso, e indica como se puede optimizar y controlar la obtención del ácido. Se hace énfasis especial en la eficiencia de oxidación del SO2(g) y como se encuentra influenciado por la composición y temperatura del gas de alimentación, la composición del catalizador, la presión del lecho catalítico, el número de perlas catalíticas y el proceso de contacto simple vs proceso de contacto doble.
Procesos de obtención
Las tres materias primas empleadas por las industrias son: azufre, aire y agua.
La fabricación de ácido sulfúrico es barata, ya que el calor que se desaprovecha en una etapa del proceso puede utilizarse en la etapa siguiente.
Antiguamente se utilizaban dos procesos para obtener ácido sulfúrico: el proceso de cámaras de plomo y el de contacto. Actualmente se usa sólo este último en todas las industrias alrededor del mundo, ya que el primero ( proceso de cámaras de plomo) desapareció debido a que se puede producir el ácido sólo en una concentración del 78%.
Proceso de contacto
El proceso se basa en el empleo de un catalizador para convertir el SO2 en SO3, del que se obtiene ácido sulfúrico por hidratación.
En este proceso, una mezcla de gases secos que contiene del 7 al 10% de SO2, según la fuente de producción de SO2 (el valor inferior corresponde a plantas que tuestan piritas y el superior a las que queman azufre), y de un 11 a 14% de O2, se precalienta y una vez depurada al máximo, pasa a un convertidor de uno o más lechos catalíticos, por regla general de platino u óxido de vanadio (V), donde se forma el SO3. Se suelen emplear dos o más convertidores.
Los rendimientos de conversión del SO_2 a SO_3 en una planta en funcionamiento normal oscilan entre el 96 y 97%, pues la eficacia inicial del 98%1 se reduce con el paso del tiempo. Este efecto de reducciones se ve más acusado en las plantas donde se utilizan piritas de partida con un alto contenido de arsénico, que no se elimina totalmente y acompaña a los gases que se someten a catálisis, provocando el envenenamiento del catalizador. Por consiguiente, en ocasiones, el rendimiento puede descender hasta alcanzar valores próximos al 95%.
En el segundo convertidor, la temperatura varía entre 500 y 600 °C. Esta se selecciona para obtener una constante óptima de equilibrio con una conversión máxima a un coste mínimo. El tiempo de residencia de los gases en el convertidor es aproximadamente de 2-4 segundos.
Los gases procedentes de la catálisis se enfrían a unos 100 °C aproximadamente y atraviesan una torre de óleum, para lograr la absorción parcial de SO3. Los gases residuales atraviesan una segunda torre, donde el SO3 restante se lava con ácido sulfúrico de 98%. Por último, los gases no absorbidos se descargan a la atmósfera a través de una chimenea.
Existe una marcada diferencia entre la fabricación del SO2 por combustión del azufre y por tostación de piritas, sobre todo si son arsenicales. El polvo producido en el proceso de tostación nunca puede eliminarse en su totalidad y, junto con las impurezas, principalmente arsénico y antimonio, influyen sensiblemente sobre el rendimiento general de la planta.
La producción de ácido sulfúrico por combustión de azufre elemental presenta un mejor balance energético pues no tiene que ajustarse a los sistemas de depuración tan rígidos forzosamente necesarios en las plantas de tostación de piritas.

La fabricación de ácido sulfúrico consta de tres etapas:
Una vez que ingresa el azufre a la planta, es depositado en un sitio denominado patio de azufre, labor que realizan ayudantes contratados por el conductor y personal de la planta. Posteriormente se inicia la transformación del azufre. Una persona denominada Operario del Fundidor, tiene la función de trasladar azufre a un compartimiento denominado Fundidor de Azufre, en donde de su estado sólido se torna líquido viscoso, ya que es sometido a altas temperaturas (150º). Con ésta iniciación de transformación del azufre se da comienzo al ciclo de producción de Ácido Sulfúrico.
Los pasos principales de proceso son:
Combustión del azufre:
Para generar dióxido de azufre (SO2)
S(s) + O2 (g) SO2(g)
Azufre Oxígeno Anhídrido
Sulfuroso
El azufre para la planta se recibe en forma sólida. El azufre se funde y clarifica antes de transferirlo a una fosa de almacenamiento de azufre limpio. Luego se bombea a un quemador de azufre donde se quema con aire suministrado por un ventilador para formar Dióxido de Azufre. Antes de entrar al quemador, el aire pasa por la torre de secado, donde se lava con ácido para retirarle el vapor de agua que contiene. La humedad del aire, si no se elimina, causará problemas en el proceso. Por ejemplo: problemas de corrosión en conductos y torres.
El aire pre-secado que entra al quemador contiene aproximadamente 21% de Oxígeno (O2) y 79% de Nitrógeno (N2). En el quemador de azufre se utiliza solamente una parte del Oxígeno del aire para quemar el azufre. La composición del gas que sale del quemador varía de acuerdo a la proporción de aire y azufre que se utilice.
Al quemar el azufre se genera una gran cantidad de calor, el cual eleva la temperatura del gas en el quemador. La temperatura alcanzada va en proporción a la concentración del gas (es decir, el porcentaje de SO2 en el gas) y también depende de la temperatura del aire que entra al quemador, así como de la cantidad de calor que se pierde en el quemador de azufre, debido a radiación del casco.
Segunda etapa; “Proceso de contacto”:
Para formar trióxido de azufre (SO3)
2SO2 (g) + ½ O2 (g) 2SO3 (g)
Anhídrido Oxígeno Anhídrido
sulfuroso sulfúrico
El SO2 que se encuentra en el gas se combina con parte del Oxígeno remanente para formar Anhídrido Sulfúrico (SO3). Para este paso, el gas debe estar a una temperatura menor que la de salida del quemador de azufre. Es necesario, por lo tanto, enfriar el gas de salida del quemador de azufre. El enfriamiento se consigue mediante una caldera de recuperación que contiene agua; el gas (SO2) caliente, que sale de la caldera de recuperación, pasa a través del filtro de gas caliente para extraerle el polvo que puede contener. Este se convierte en (SO3) en el convertidor, el cual contiene cuatro capas de catalizador que hace que la reacción química se produzca a velocidad mucho mayor que si no se utilizara el catalizador, éste no se afecta ni se agota.
Esta reacción es exotérmica y también reversible (es decir, que no llega a completarse), la temperatura de entrada del gas a cada a paso del convertidor debe mantenerse en el nivel correcto con el fin de conseguir la conversión requerida. El gas es enfriador entre cada paso para mantener la temperatura correcta de entrada a cada paso.
Después del segundo paso el gas pasa a través del intercambiador caliente de paso intermedio, el cual enfría el gas y también sirve para precalentar el gas que retorna de la torre de absorción intermedia hacia el cuarto paso de catalizador. Después del tercer paso el gas es conducido a la torre barredora (para extraerle el selenio), y luego a la torre de absorción intermedia, donde el SO3 que contiene el gas es absorbido en Ácido Sulfúrico del 98%. El gas es enfriado antes de la torre en el intercambiador frío; el intercambiador frío de paso intermedio también sirve para calentar el gas que retorna de la torre de absorción intermedia, para lograr la temperatura correcta al cuarto paso. El SO2 que queda en el gas es luego convertido en SO3 en el cuarto paso, el gas que sale del convertidor pasa a través del economizador supercalentador, donde es enfriado antes de pasar a la torre de absorción final, donde el SO3 remanente es absorbido en Ácido Sulfúrico del 98%.
- El pentóxido de Vanadio (V2O5) es el catalizador que se utiliza en este 2º paso. Como las moléculas de dióxido de azufre y de oxígeno reaccionan en contacto con la superficie del pentóxidodeVanadio sólido, el proceso se denomina: ”proceso de contacto”.
Tercera etapa:
Para formar una solución que contiene 98 a 99% de Ácido Sulfúrico.
SO3 (g) + H2O(l) H2SO4 (ac)
Anhídrido Agua Ácido
sulfúricosulfúrico
El gas SO3 producido en el convertidor, aunque adecuadamente enfriado, no se combinará directamente con agua, sino que debe combinarse indirectamente mediante absorción en Ácido Sulfúrico de 98-99%. En estas condiciones el SO3 se une fácilmente con el agua contenida en el Ácido. Esta operación se lleva a cabo en las torres de absorción donde se efectúa la absorción del SO3 en dos etapas, la primera antes que la conversión a SO3 se haya completado, denominado ínter absorción. El SO3 absorbido en la torre intermedia sigue hacia adelante y el restante es absorbido en la torre de absorción final (segunda etapa).
El Ácido que recircula por la torre de secado se debilita con el vapor de agua que le quita el aire, mientras que en las torres de absorción el Ácido se refuerza mediante la absorción del gas SO3; el Ácido más débil se combina con el Ácido reforzado proveniente de las torres de absorción antes de ingresar a la torre de enfriamiento. La adición de agua a las corrientes combinadas también es necesaria para mantener la concentración adecuada del Ácido para lograr la absorción del SO3 y un buen secado.
El flujo de Ácido combinado es bombeado a través de los enfriadores de Ácido antes de recircular el Ácido a la torre de secado y las torres de absorción. La absorción del vapor de agua por el Ácido circulante de secado, además de la adición de agua a las corrientes combinadas de Ácido de las torres de secado final y paso intermedio, ha aumentado constantemente el volumen del Ácido dentro del tanque común de bombeo; como resultado de esto, constantemente se bombea Ácido de 98-99% desde el sistema común de secado final e intermedio al tanque de almacenamiento.
PROCESO DE CAMARAS DE PLOMO
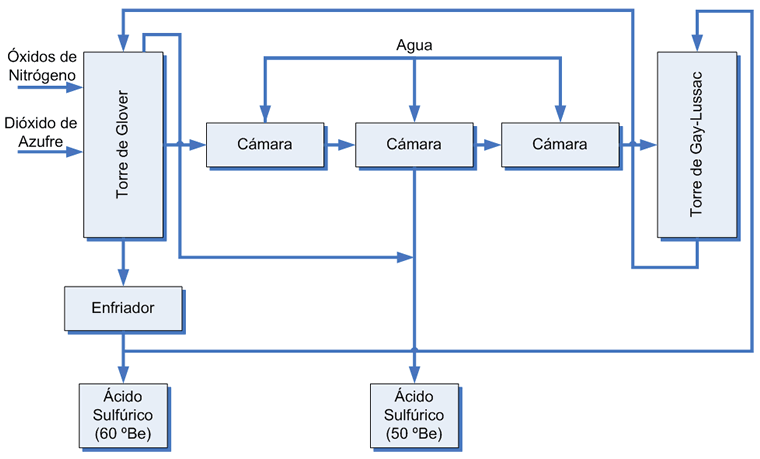
Se llama así porque los recipientes donde tiene lugar la hidroxilación de SO2 son enormes depósitos formados por planchas de plomo. La reacción en su forma más sencilla, está indicada por estas igualdades:
SO2 (g) + O (g) SO3 (g)
Anhídrido Oxígeno Anhídrido
sulfuroso sulfúrico
SO3 (g) + H2O(l) H2SO4 (ac)
Anhídrido Agua Ácido
sulfúricosulfúrico
En el proceso de cámaras de plomo óxido de azufre (IV) (SO2) gaseoso caliente entra por la parte inferior de un reactor llamado torre de Glover donde es lavado con vitriolo nitroso (ácido sulfúrico con óxido nítrico (NO) y óxido de nitrógeno (IV) (NO2) disueltos en él), y mezclado con óxido de nitrógeno (NO) y óxido de nitrógeno (IV) (NO2) gaseosos. Parte de óxido de azufre (IV) es oxidado a óxido de azufre (VI) (SO3) y disuelto en el baño ácido para formar el ácido de torre o ácido de Glover (aproximadamente 78% de H2SO4).
De la torre de Glover una mezcla de gases (que incluye óxido de azufre (IV) y (VI), óxidos de nitrógeno, nitrógeno, oxigeno y vapor) es transferida a una cámara recubierta de plomo donde es tratado con más agua. La cámara puede ser un gran espacio en forma de caja o un recinto con forma de cono truncado. El ácido sulfúrico es formado por una serie compleja de reacciones; condensa en las paredes y es acumulado en el piso del la cámara. Pueden existir de tres a seis cámaras en serie, donde los gases pasan por cada una de las cámaras en sucesión. El ácido producido en las cámaras, generalmente llamado ácido de cámara o ácido de fertilizante, contiene de 62% a 68% de H2SO4.
Luego de que los gases pasaron por las cámaras se los hace pasar a un reactor llamado torre de Gay-Lussac donde son lavados con ácido concentrado enfriado (proveniente de la torre de Glover). Los óxidos de nitrógeno y el óxido de azufre (IV) que no haya reaccionado se disuelven en el ácido formando el vitriolo nitroso utilizado en la torre de Glover. Los gases remanentes son usualmente liberados en la atmósfera.
ACETILENO
El acetileno o etino es el alquino más sencillo. Es un gas, altamente inflamable, un poco más ligero que el aire e incoloro. Produce una llama de hasta 3.000º C, la mayor temperatura por combustión hasta ahora conocida.
Características
El acetileno es un compuesto exotérmico. Esto significa que la descomposición en sus elementos libera calor. Por esto su generación suele necesitar elevadas temperaturas en alguna de sus etapas o el aporte de energía química de alguna otra manera.
El acetileno es un gas explosivo si su contenido en aire está comprendido entre 2 y 82%. también explota si se comprime solo, sin disolver en otra sustancia, por lo que para almacenar se disuelve en acetona.
Obtención del acetileno
En petroquímica se obtiene el acetileno por quenching (el enfriamiento rápido) de una llama de gas natural o de fracciones volátiles del petróleo con aceites de elevado punto de ebullición. El gas es utilizado directamente en planta como producto de partida en síntesis; un proceso alternativo de síntesis, más apto para el laboratorio, es la reacción de agua con carburo cálcico (CaC2). Se forma hidróxido cálcico y acetileno. El gas formado en esta reacción a menudo tiene un olor característico a ajo debido a trazas de fosfina que se forman del fosfuro cálcico presente como impureza.
El Acetileno (Etino) [C2H2] se obtiene por medio de la reacción de hidrólisis de carburo de calcio [CaC2]. Loque sucede en esta reacción es que los dos carbonos que están enlazados con el calcio, se saturan con doshidrógenos y ocurre una reacción de desplazamiento donde se crea un hidróxido en relación con el agua. Loscarbonos rompen el enlace con el calcio y se unen entre si creando un triple enlace (Acetileno (etino) [C2H2])el calcio que queda con dos valencias libres se uno con los dos hidróxidos formados en una enlace sencillo.
ALCOHOL ETILICO
El compuesto químicoetanol, conocido como alcohol etílico, es un alcohol que se presenta como un líquido incoloro e inflamable con un punto de ebullición de 78 °C.
Mezclable con agua en cualquier proporción; a la concentración de 95% en peso se forma una mezcla azeotrópica.
Su fórmula química es CH3-CH2-OH, principal producto de las bebidas alcohólicas como el vino (alrededor de un 13%), la cerveza (5%) o licores (hasta un 50%).
El etanol es un liquido incoloro y volátil que está presente en diversas bebidas fermentadas. Desde la antigüedad se obtenía el etanol por fermentaciónanaeróbica de una disolución con contenido en azúcares con levadura y posterior destilación.
Dependiendo del género de bebida alcohólica que lo contenga, el etanol aparece acompañado de distintos elementos químicos que lo dotan de color, sabor, olor, entre otras características.
Las materias primas más utilizadas y económicas, son las que se originan en la caña de azúcar:
Jugo, miel A, miel B, y melaza; utilizándose más extensamente el jugo y la melaza considerada un residuo de los ingenios azucareros y de la cual se puede obtener un buen porcentaje de alcohol.
La melaza es un líquido denso de coloración obscura y su composición es muy variable de acuerdo con la variedad de la caña, la edad, sanidad, maduración, quema, etc.
OBTENCIÓN DEL ALCOHOL ETÍLICO
Destilación
Para obtener etanol libre de agua se aplica la destilación azeotrópica en una mezcla con benceno o ciclohexano. De estas mezclas se destila a temperaturas más bajas el azeótropo, formado por el disolvente auxiliar con el agua, mientras que el etanol se queda retenido. Otro método de purificación muy utilizado actualmente es la absorción física mediante tamices moleculares. A escala de laboratorio también se pueden utilizar desecantes como el magnesio, que reacciona con el agua formando hidrógeno y óxido de magnesio.
FERMENTACIÓN
La fermentación es un proceso metabólico energético que comprende la descomposición de moléculas, tales como carbohidratos, de manera anaerobia. La fermentación ha sido utilizada desde tiempos antiguos en la preparación de alimentos y bebidas. El desarrollo químico ha revelado la naturaleza biológica del proceso de fermentación. El producto de la fermentación es el alcohol etílico, pequeñas cantidades de propanol, butanol, ácido acético, y ácido láctico; los alcoholes de alta concentración también se pueden formar. El alcohol etílico está familiarizado con las bebidas alcohólicas. En su forma no natural es usado como un solvente industrial y como materia prima para la manufactura de acetaldehido, acetato etílico, ácido acético, dibromito de etileno, glicol y muchos otros químicos orgánicos. El alcohol puro también puede ser utilizado para propósitos medicinales, farmacéuticos y saborizantes.
La fermentación del alcohol etílico es realizada en forma cerrada por cualquier carbohidrato rico en substratos. La melaza, licor producido de desechos, permanecen después de la cristalización de la sucrosa y es usada ampliamente como materia prima en la fermentación alcohólica. La melaza blackstrap contiene 35-40% de sucrosa y 15-20% de azúcares invertidos (glucosa y fructuosa) La melaza hightest contiene 21-22% de sucrosa y 50-55% de azúcares invertidos. La mayoría de las melazas blackstrap no requieren otros nutrientes adicionales para realizar la fermentación del alcohol etílico. Sin embargo, las melazas hightestrequieren cantidades considerables de sulfato de amonio y otras sales, como fosfatos. El contenido de nutrientes no azucarados de 50-lids de las melazas hightestes aproximadamente 7%, comparado con el 28-35% encontrado en las melazas blackstrap.
El alcohol etílico también puede ser producido por fermentación del almidón, suero o licor de desechos de sulfito. La fermentación de granos requiere un pretratamiento dado que la levadura no puede metabolizar directamente el almidón. Los granos (usualmente el maíz) son agrupados y calentados en una lechada acuosa para gelatinizar o solubilizar el almidón. Algunas enzimas líquidas pueden ser añadidas a bajas temperaturas. El almidón líquido es enfriado alrededor de 65°C y tratado con amilasa de malta o de hongos para convertir el almidón en oligosacáridos. Luego, la levadura es añadida junto con amiloglucosidasa (o glucoamilasa) los cuales convierten los oligosacáridos en glucosa. El proceso de fermentación y refinación posteriores son los mismos que se realizan cuando se usa melaza como materia prima.
La producción del alcohol etílico es realizada a través de procesos eficientes y automáticos. El proceso de manufactura no es muy complejo y es fácil de realizar. El control de la contaminación y el mantenimiento y reparación de las maquinarias y equipos también son fáciles. Aquellas naciones con climas tropicales y sub-tropicales, con abundante producción de azúcar y maíz, podrían invertir en el establecimiento de esta planta de producción que puede ser orientada tanto a la exportación como a la importación.
1. Transporte y almacenamiento de la melaza: La melaza obtenida desde una fábrica proveedora es transportada vía transferencia de tuberías o carros de almacenamiento a la planta de procesamiento de alcohol etílico. La melaza es colocada en un tanque de almacenamiento de concreto bajo tierra por bombeo de la melaza. Cuando el proceso ha comenzado, la melaza almacenada será bombeada en un contenedor o vasija de disolución para ajustarlo a una concentración adecuada.
2. Preparación de la melaza: La melaza es bombeada dentro del tanque medidor a través de un bombeo desde el tanque bajo tierra el cual recibe el material directamente desde el tanque de almacenamiento por transferencia de tuberías. Después que la melaza es medida exactamente, fluye hacia el tanque de disolución de la melaza. Debido a su resistente concentración de azúcar, la melaza no soporta una fermentación directa, por lo tanto primero debe ser diluido a la concentración deseada. Este es llamado masa o templa, y presenta los carbohidratos listos para la inoculación o vacunación de los cultivos de semillas. La melaza utilizada en este proceso no necesita ser esterilizada o “nutriotinizada” por un proceso diseñado especialmente, el cual será útil para eliminar el consumo de vapor y los costos de producción de corte. Después que la melaza es diluida a la concentración deseada, una mezcladora automática ayudará a darle una concentración homogénea para el proceso de fermentación, antes de que sea bombeado a una serie de fermentadores de acero.
3. Estación de cultivo de granos: La estación es equipada con un fermentador piloto en conjunto con el equipo de cultivo de granos y los instrumentos de cultivo diseñados especialmente. Este proceso es realizado bajo una exacta supervisión de laboratorio, incluyendo la selección de la inoculación de los granos de levadura, la adición de nutrientes, el ajuste del pH, el control de temperatura, y finalmente la limpieza y esterilización de la máquina de cultivo de levadura para la realización del siguiente lote.
4. Suministro de agua procesada: El equipo suministrador de agua procesada y el equipo incrementador de presión son proporcionados. El suministro de agua procesada será diseñado para una carga máxima de 21 TM/Hr; sin embargo, sólo aproximadamente 210 TM es necesario diariamente. El agua utilizada en el proceso podría ser tratada como agua drenada de calidad o suministrado por un pozo de 90-100 metros de profundidad.
5. Estación de fermentación: Existen 8 fermentadores con una capacidad aproximada de 45 KL. Los fermentadores están conectados por tuberías para una operación de fermentación continua. Esta estación tiene un control automático de temperatura, velocidad de flujo, operación de templado y operación de alimentación. Usualmente el ciclo de fermentación dura de 2-3 días. Dado que el alcohol etílico es formado por levadura desde monosacárido, es necesario descomponer la sucrosa en d-glucosa y d-fructuosa. Las enzimas producidas por la levadura cambian los monosacáridos en alcohol y dióxido de carbono. Después que ha sucedido la reacción, el alcohol etílico presente en los fermentadores puede ser separado por destilación. El contenido de alcohol de la masa es de 7-12% de su volumen, es bombeada hasta la sección de destilación del alcohol. Después de pasar a través de varios intercambiadores de temperatura, el residuo en la base del destilador transporta proteínas, residuos de azúcar y otras impurezas que pueden ser extraídas y usadas como componentes para alimento animal. El diseño de la estación elimina los errores de operación y puede alcanzar resultados efectivos a bajos costos de operación. La capacidad de esta estación puede presentar el requerimiento para la manufactura suficiente del caldo fermentado para la estación de destilación con una producción diaria de 30 KL de alcohol etílico.
6. Estación de destilación y rectificación: El caldo conteniendo alcohol etílico, agua, aldehido, ácido acético, etc. , pasa a través de un intercambiador de temperatura hacia un condensador parcial para mantener el alcohol en la columna y para proporcionar un reflujo para las placas superiores. Los productos más volátiles, los cuales todavía pueden contener rastros de aldehidos y alcohol, son condensados completamente y transportados detrás de la parte superior del destilador de aldehido. Cerca de la parte superior de la columna, el 95-96% del alcohol es absorbido a través del condensador para su almacenamiento.

Proceso a partir de caña de azúcar
Acondicionamiento
El acondicionamiento consiste de un lavado inicial de lacaña con agua a 40ºC y posteriormente una molienda otrituración donde se extrae el jugo azucarado con agua a60ºC, retirando como subproducto el bagazo con uncontenido en fibra de alrededor del 46%, que puede serutilizado en la generación de vapor.
El jugo de caña obtenido se somete a un proceso declarificación en el que se le agrega óxido de calcio y unapequeña porción de ácido sulfúrico con el fin dedisminuir el pH a 4,5 y provocar la hidrólisis de lasacarosa en hexosas. En el recipiente clarificador seprecipita un lodo, que debe ser retirado y enviado a unfiltro otatorio al vacío. De este filtro se obtiene una tortaconocida como cachaza y un filtrado que es retornado alrecipiente de clarificación. Finalmente el jugoproveniente de la clarificación es esterilizado a 105ºC yenviado a la fermentación, a la cual debe ingresar con uncontenido en azúcares entre 130-180 g/L.
Fermentación
En esta etapa se lleva a cabo la fermentación de glucosa yuna parte de la fructosa en etanol y dióxido de carbono,mediante la levadura Saccharomycescerevisiaeque escontinuamente recirculada desde una centrífuga ubicadaaguas abajo del fermentador. Además de la producciónde etanol se tuvo en cuenta la producción en formaestequimétrica de biomasa y otras sustancias comoacetaldehído, glicerol y alcoholes de fusel. Los gasesformados en la fermentación son retirados y enviados auna torre de adsorción en la cual se debe recuperar el98% en masa del etanol arrastrado.
Separación y deshidratación
La destilación y la adsorción con tamices moleculares seusan para recuperar el etanol del caldo de fermentaciónobteniéndose etanol a 99,5% en peso de pureza. Ladestilación se lleva a cabo en dos columnas, la primeraremueve el CO2 disuelto (que es enviado a la torre deabsorción) y la mayoría del aguaobteniéndose undestilado con 50% en peso de etanol y unos fondos conuna composición inferior al 0,1% en peso; en estacolumna se alimenta junto al caldo de fermentación eletanol recuperado en la absorción proveniente de losgases de fermentación.
El agua restante es removida de la mezcla medianteadsorción en fase vapor en dos lechos de tamicesmoleculares. El producto de la regeneración de lostamices es recirculado a la segunda columna dedestilación.
Tratamiento de efluentes
De las aguas de residuo en el proceso de obtención deetanol a partir de caña de azúcar las de mayor volumenson aquellas que provienen de los fondos de la primeracolumna de destilación, conocidas como vinazas. Eltratamiento propuesto consiste en su evaporación y posterior incineración. La función del tren deevaporación (cuatro efectos) es concentrar los sólidossolubles y demás componentes poco volátiles presentes en las inazas hasta un valor cercano al 12% en peso, yaque en esta concentración se hacen aptas para suincineración. Los condensados de los evaporadoresson recolectados junto con los fondos de la segundacolumna de destilación y utilizados como agua de proceso.